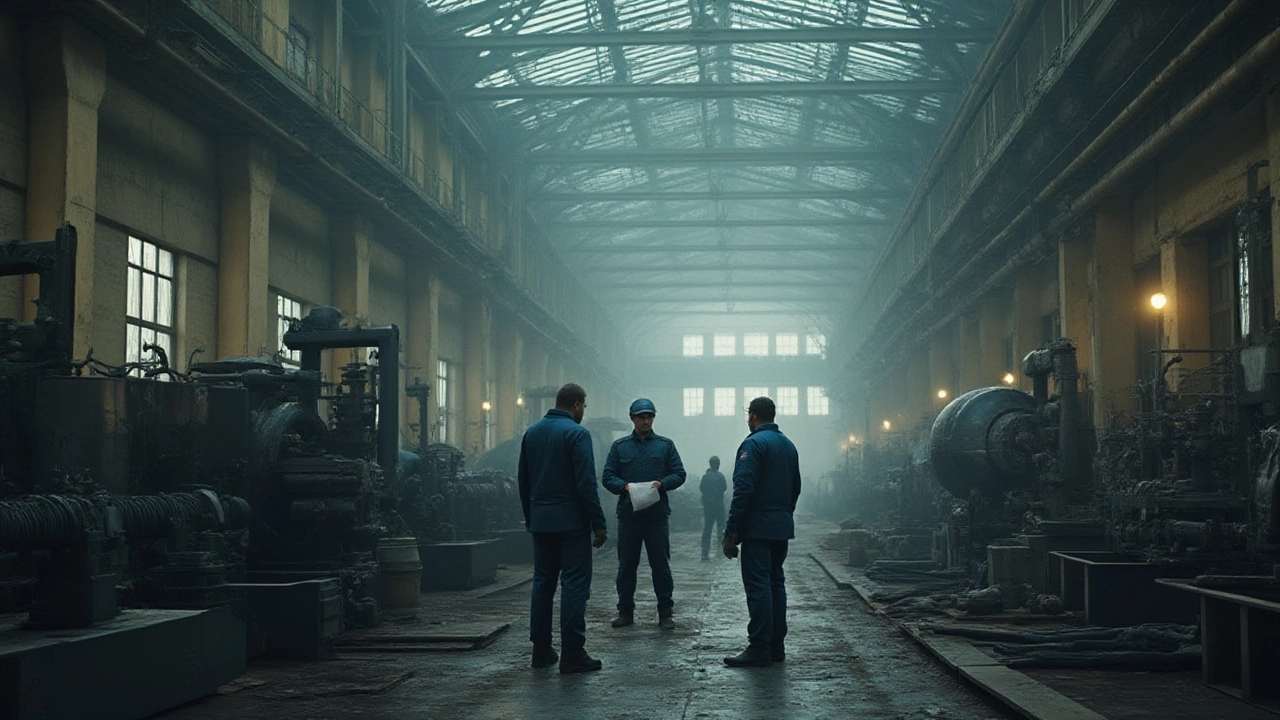
Рынок машиностроения сегодня напоминает огромный двигатель, в котором порой не хватает деталей для слаженной работы. Вроде бы, технология есть, грамотные специалисты остались, да и рынок не исчез — но что-то тормозит весь этот мощный аппарат. За последние 10 лет в России каждая третья машиностроительная компания хоть раз сталкивалась с нехваткой узлов или комплектующих из-за перебоев поставок. Компаний, которым не хватает рабочих рук, стало примерно на 47% больше, если сверить свежие данные от РСПП с теми, что были в 2018. Только кажется, что цифровизация решает всё: в реальности почти треть отрасли работает на оборудовании старше 20 лет. Давайте поговорим, какие проблемы разрывают этот сложный механизм сегодня и что на практике делают заводы, чтобы двигаться вперёд.
Стереотипы о заводах, где всё валится из рук, давно не актуальны. Да, на крупных предприятиях в Тольятти или Екатеринбурге работают роботы, на линии стоят станки с ЧПУ, а инженеры проектируют детали прямо в 3D. Но на другом полюсе отрасли ― сотни заводов среднего и малого масштаба мучаются с устаревшим оборудованием и банальным отсутствием квалифицированных рабочих. Одна из самых ощутимых проблем — кадровый голод. За последние три года спрос на инженеров-механиков и токарей вырос почти вдвое по данным платформы HeadHunter, а средний возраст специалиста иногда зашкаливает за 50.
Вторая боль машиностроения — это крепкая зависимость от импортных комплектующих. После 2022 года понадобилось срочно искать замены электронным модулям и подшипникам, когда прежние поставки обрывались буквально за ночь. Импортозамещение шло через серьёзную головную боль: в России нет локальных аналогов многих деталей высокой точности. Согласно исследованию Минпромторга, у более 60% компаний отрасли в течение 2023 года возникали перебои в снабжении сложных компонентов. Даже если есть чертёж, производство штучной детали под заказ в разы дороже массовой закупки из-за рубежа.
Еще одна преграда — оборудование. Почти треть предприятий по данным АЦ при Правительстве РФ работает на станках, чей возраст превысил 20 лет. Переход на современные линии часто требует капвложений от 50 миллионов рублей для средних игроков — и не факт, что они окупятся в условиях нестабильного спроса. Добавьте к этому сложности с обучением персонала: когда на завод приводят новый обрабатывающий центр, часто приходится отправлять людей учиться чуть ли не за свой счет или обращаться к дорогим сторонним специалистам.
Технологические обновления иногда спотыкаются об инфраструктурные «узлы»: нестабильное электроснабжение, нехватка новых цехов, банальная нехватка площадей под лаборатории и отделы ОТК. Физически и морально устаревшие здания не всегда подходят под новые экостандарты. Вот вам простой пример — на одном из заводов Подмосковья обновление вентиляции и электросетей заняло больше года и обошлось дороже, чем покупка нового станка.
Добавьте к этому сложности с логистикой: перевозка крупногабаритных изделий требует спецтранспорта, а издержки за последний год выросли почти на 30% после скачка цен на ГСМ и жестких ограничений по тоннажу.
Импортозамещение долго воспринималось как формальность — мол, поменяем наклейку и дело сделано. Но в 2022-2025 годах пришло понимание: просто собрать изделие из «российских» деталей не всегда возможно даже технически. По данным Ассоциации машиностроителей России, только 32% оборудования, применяемого сейчас в отрасли, собрано из полностью отечественных комплектующих. Остальные «собираются» из всего, что доступно: европейская, китайская или индийская сборка.
Производители электронных узлов оказались в самой уязвимой позиции. Модуль управления или сенсорные панели — все это требует программных обновлений, которые раньше легко заказывали у немецких или японских поставщиков, теперь приходится разрабатывать с нуля или сливать заказы специфическим интеграторам внутри страны. И даже если удается всё собрать, на испытания и тесты уходит месяцы.
У российских конструкторских бюро появился шанс войти в историю, разрабатывая новые узлы для «отечественных» ЧПУ, однако проблема кадров и финансирования стоит остро. Средний цикл создания нового продукта с «чистого листа» — не менее 18-24 месяцев. За это время технология на мировом рынке может устареть.
Интересно, что машиностроители активно используют партнерства с университетами. Например, «КамАЗ» сотрудничает с КНИТУ в рамках локализации более 70% комплектующих. Но по статистике Минобрнауки, на реальное внедрение разработок приходится только около 10% совместных проектов: остальные «зависают» из-за нехватки бюджетов или устаревшей техдокументации.
Год | Доля отечественных компонентов, % | Доля зарубежных компонентов, % |
---|---|---|
2018 | 24 | 76 |
2021 | 31 | 69 |
2024 | 39 | 61 |
Как видно, прогресс есть, но он идет медленно. Фокус смещается в сторону технологий двойного назначения, чтобы ускорить внедрение новых решений за счет госфинансирования и налоговых льгот для разработчиков.
Автоматизация — классный лозунг, но воплощение на заводе больше похоже на шахматную партию, где ставка на одно неверное решение может отбросить назад на годы. Напрямую на старых заводах внедрять цифровые продукты сложно: умные датчики требуют специальной инфраструктуры, а их интеграция под старый парк обходится дорого и не всегда дает быструю отдачу.
Всё чаще предприятия делают ставку на так называемую «гибридную» цифровизацию: где-то внедряют MES системы для управления производством, а где-то просто переходят с бумажных маршрутов на планшеты. Как подтверждают данные национального проекта «Производительность труда», за 2024 год предприятия, где активно внедряли электронные карты, смогли повысить скорость обработки заказов на 18%. Для небольшого цеха это плюс неделя к производственному циклу за год.
Реальный кейс: на одном из заводов по выпуску станков в Самарской области внедрили модуль электронной очереди для поставщиков и добились сокращения простоев на отгрузке с 4 дней до 11 часов. Такие штуки не требуют огромных капиталовложений, зато мгновенно экономят ресурсы.
Но есть и обратная сторона. Внедрение роботов и автоматизированных линий не всегда возвращается сторицей. По данным Единого реестра инвестпроектов РФ, до 60% предприятий, купивших роботов в кредит, сталкиваются с трудностями при возврате инвестиций: увеличение затрат на обслуживание, дефицит специалистов по ремонту, да и настройка оборудования требует длительной адаптации персонала.
Что ещё мешает автоматизации? Слабая доступность современных ИТ-решений, их высокая стоимость и несовместимость с устаревшими системами управления. А ведь до сих пор на многих заводах цифровые отчеты ведутся в архаичных EXCEL-файлах, а согласование заказа может тянуться до 3 рабочих дней.
Что советуют эксперты, если автоматизации не хватает ресурсов? Как минимум — начинать с оптимизации логистики, запасов и проектирования, постепенно переходя к более сложным цифровым инструментам.
Проблема квалифицированных кадров мощнее любой технической. Новое оборудование без грамотного персонала — всё равно что спорткар без бензина. По опросу РСПП, около 58% руководителей машиностроительных предприятий открыто заявляют о нехватке специалистов, особенно среднего звена (наладчики, мастера участка). Спрос на инженеров-программистов с опытом работы в 3D CAD вырос на 60% за последние три года. А выпускники профильных вузов зачастую не владеют новыми цифровыми технологиями школьного уровня, потому что программы ориентированы на архаичные ГОСТы и «бумажную» работу.
Система дуального образования только начинает набирать обороты в промышленности: по сути, это когда студенты сначала работают на заводе, а потом учатся по тематическим программам университетов, ломая привычную систему. Например, в Санкт-Петербурге на одной из машиностроительных площадок набрали экспериментальную группу студентов для быстрой подготовки специалистов по программированию роботов-манипуляторов. Итог: из 20 человек только 3 остались в профессии через год из-за низкой оплаты, высокого входного порога, а главное — отсутствия понятной карьерной траектории.
Механизмы поощрения тоже работают со скрипом: на многих заводах нет чёткой системы роста зарплат, дефицит наставников не позволяет быстро передавать опыт, а внутреннее обучение воспринимается лишь как формальный процесс. На одной из площадок в Подмосковье попытались мотивировать работников конкурсами — победителей отправляли на стажировки за границу, но после 2022 года этот стимул потерял свою актуальность.
Что может исправить ситуацию? Прозрачная система наставничества, сильная интеграция со школами и колледжами, стимулирование молодых специалистов быстрым карьерным ростом. Кроме того, обязательные стажировки на заводах для студентов с первой-второй недели учёбы, а не в виде летних практик на бумаге, дают реальное понимание процессов и помогают адаптироваться к реальной заводской жизни.
Компании, для которых проблема особо остра — могут попробовать привлекать специалистов из смежных отраслей (например, авиации или судостроения), регулярно отправлять инженеров на краткосрочные курсы и проводить собственные внутренние чемпионаты профмастерства, что иногда дает толчок к закреплению кадров лучше всяких премий.
Теперь о самом интересном — что реально помогает бизнесу держаться на плаву, несмотря на все сложности? Крупные предприятия все чаще ставят на гибридные производственные цепочки — само производство локализуют по максимуму, а критичные детали ищут по всему миру, не ограничиваясь политикой санкций, а используя параллельный импорт и локальных интеграторов.
Один интересный лайфхак из опыта небольших машиностроительных фирм — проработка поставщиков запчастей не меньше, чем проработка собственной продукции. Те, кто в 2022 перешёл к многоуровневой системе поиска запчастей и использовал «маркетплейсы» для промышленных закупок, потеряли на простоях втрое меньше времени, чем те, кто искал детали только по старым контактам.
Ещё один работающий метод — создание небольших инкубаторов внутри завода. Туда привлекают команду технологов, проектировщиков и айтишников, которые на маленьких проектах пробуют, как можно удешевить, ускорить и упростить отдельные узлы оборудования. Опыта, конечно, тоже набираются. Обычно такие инкубаторы приносят экономию затрат на 7-14% в год, а успешные кейсы масштабируют на все подразделения.
Система обмена опытом с другими предприятиями — в формате производственных командировок, «дней открытых дверей» для инженеров и челленджей по обмену лайфхаками — дает больше реальных результатов, чем скучные отраслевые конференции. Например, уральские заводы по своим каналам распространяют опыт быстрой замены импортных подшипников на локальные аналоги и делятся «живыми» списками надёжных поставщиков, что реально экономит месяцы поиска.
Финальный совет: смотрите не только на крупные тренды, а разрабатывайте свои маленькие решения, которые решают конкретные проблемы вашего предприятия «здесь и сейчас». Только так машиностроительный комплекс сможет справиться с вызовами — не ожидая чарующего будущего, а действуя уже сегодня.
Я работаю в области производства, специализируясь на машиностроении. Мне нравится исследовать новые подходы в проектировании и улучшении процессов. Пишу статьи и доклады на темы, связанные с прогрессом в машиностроении. Это дает мне возможность делиться своими знаниями и опытом с широкой аудиторией. Моя цель — сделать вклад в развитие современных технологий.
Написать комментарий