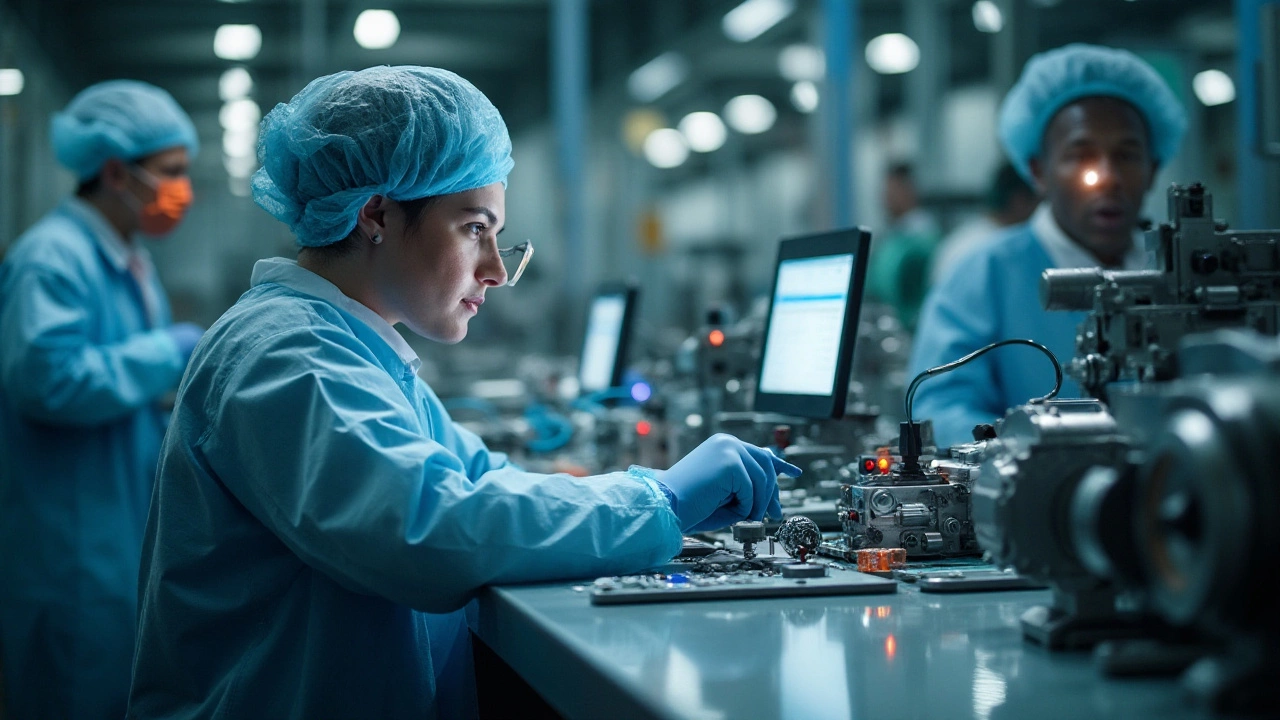
Контроль качества в машиностроении — это важнейший элемент успешного производства. Он помогает гарантировать, что каждая деталь и механизм соответствуют строгим стандартам безопасности и надежности.
В нашей статье мы подробно рассмотрим три основные вида контроля, которые используются на предприятиях машиностроения. Каждый из них имеет свои задачи и время проведения, что позволяет интегрировать их в производственный процесс с максимальной эффективностью.
Входной контроль — это первая линия обороны в процессе управления качеством в машиностроении. Его основной задачей является проверка материалов и комплектующих, поступающих на предприятие. Только представьте: если на этой стадии что-то пойдет не так, всё производство может столкнуться с серьезными проблемами. Дефектные или несоответствующие спецификациям материалы не просто приводят к потерям времени и денег, но и рискуют снизить качество конечного продукта. Поэтому так важно уделять большое внимание этой стадии, внедряя строгие и эффективные методы контроля.
На практике входной контроль реализуется через серию проверок и тестов. Например, применение современных технологий позволяет проводить неразрушающие методы контроля, что характерно для высокотехнологичных отраслей. Это включает использование рентгеновских установок, ультразвукового тестирования и даже анализа с помощью компьютерной томографии, чтобы гарантировать соответствие материалов требуемым стандартам.
Особую роль в процессе входного контроля играет сотрудничество с надежными поставщиками. Часто такие партнеры предоставляют необходимые сертификаты качества и соответствия стандартам, таким как ISO или ГОСТ. В крупных производственных комплексах входной контроль может быть автоматизирован, где каждая партия материалов проверяется при помощи встроенных систем. Это дает возможность не просто экономить время, но и минимизировать ошибки, связанные с человеческим фактором. Как говорил Томас Эдисон:
«Качество означает делать все правильно, даже когда никто не смотрит».
Важно отметить, что внедрение системы входного контроля требует инвестиций и обучения сотрудников, однако в долгосрочной перспективе это позволяет избежать значительно больших затрат на исправление дефектов и возврат бракованной продукции. Этот этап является критическим в цепочке управления качеством и без него успешное производство становится почти невозможным. Снижение ошибок на ранних стадиях производства экономит массу ресурсов и энергии на последующих этапах. Внимание к деталям в контроле качества на этапе входа обеспечивает стабильность и надежность на выходе.
Операционный контроль в машиностроении — это ключевой этап, который осуществляется в процессе производства изделий. Он играет центральную роль в обеспечении стабильности и качества выпускаемой продукции. Контроль проводится непосредственно на каждом производственном участке, чтобы оперативно выявлять и устранять дефекты в процессе их возникновения.
Процесс операционного контроля может варьироваться в зависимости от специфики предприятия и типа производимых изделий. Однако основная цель остаётся неизменной — обеспечить своевременное соответствие продукции установленным стандартам качества. Для этого часто используются такие методы как проверка критических параметров на каждом этапе сборки, тестирование отдельных компонентов и систем, а также контрольные испытания готовых изделий.
Особое внимание уделяется работе операторов и инженеров, которые могут использовать автоматизированные системы управления процессами. Эти системы способны не только фиксировать отклонения, но и автоматически корректировать процессы в режиме реального времени. Такие технологии позволяют значительно сократить количество брака и увеличить производительность труда.
На некоторых предприятиях внедряются системы статистического контроля качества (СКК), которые помогают анализировать данные и выявлять причины возникновения дефектов. Это позволяет не только реагировать на конкретные проблемы, но и предотвращать их на ранних стадиях. Известный эксперт в области качества Д. М. Джуран отметил:
«Сектор статистического управления качеством дает возможность понять, какие именно изменения происходят в производственном процессе, и, что более важно, насколько они существенны».
Несмотря на наличие различных технологий и средств, человеческий фактор остаётся важным элементом операционного контроля. Опытный оператор способен выявить проблему там, где автоматизация может не распознать отклонения. В этом контексте особую роль играют тренировки и повышение квалификации персонала.
Значимость операционного контроля подчёркивается не только улучшением качества, но и экономией ресурсов. Минимизация брака и снижение потерь на каждом этапе производственного процесса позволяют значительно уменьшить расходы на исправление дефектов и переработку изделий.
Важно отметить, что успешное проведение операционного контроля требует чёткой документации и строгого соблюдения технологических карт. Без их соблюдения невозможно обеспечить запланированное качество продукции. Таким образом, операционный контроль можно с уверенностью назвать «первой линией обороны» в системе управления качеством.
Выходной контроль — это последний рубеж в системе управления качеством, в том числе и в машиностроении. На данном этапе проверяется соответствие готовых изделий установленным стандартам и техническим требованиям, а также ожиданиям заказчика. Выходной контроль играет важную роль в поддержании репутации компании, так как именно от его результатов зависит, с каким уровнем качества продукция поступит к потребителю.
Осуществление выходного контроля включает в себя ряд определенных процедур. Во-первых, продукция проверяется на отсутствие физических дефектов, таких как трещины или несоответствия в размерах. Во-вторых, технологические характеристики изделий, включая их работоспособность и долговечность, должны быть в пределах допуска. Эти проверки могут проводиться как в лабораториях, так и на специальных стендах, в зависимости от сложности продукции и требований клиента.
Интересный факт: выходной контроль позволяет не только выявить недочеты, но и проанализировать их причины. Благодаря этой информации предприятие может совершенствовать свои производственные процессы. По данным исследования Национального института качества, предприятия, уделяющие должное внимание выходному контролю, сокращают количество возвратов продукции более чем на 20%. В этом случае не нужно забывать о важной роли обучения сотрудников, работающих на этапе контроля. Ведь их квалификация напрямую влияет на точность и эффективность проводимых проверок.
Практика показывает, что внедрение выходного контроля может заметно улучшить имидж компании.
"Качество — это не просто выполнение работы как надо, а источник уверенности для наших клиентов", — отметил известный эксперт по качеству Эдвард Деминг.Тем не менее, стоит учитывать, что слишком жесткий контроль может привести к увеличению времени и производственных затрат. Поэтому необходимо находить баланс между тщательностью проверок и экономической эффективностью. Здесь может помочь использование современных технологий, таких как автоматизированные системы проверки, которые помогают ускорить процесс и сократить вероятность человеческой ошибки.
Таким образом, роль выходного контроля в контроле качества трудно переоценить. Он является не только последним этапом защиты от недостатков продукции, но и отражением общих стандартов качества всей организации. Эффективное выполнение выходного контроля способствует укреплению доверия клиентов и повышению конкурентоспособности компании на рынке. И хотя реализация этой системы требует определенных вложений и усилий, она стоит того, чтобы придерживаться высоких стандартов в любой области производства.
Для успешного внедрения системы контроля качества в машиностроении необходимо учитывать множество факторов. Одним из ключевых моментов является подготовка персонала. Инженеры и операторы должны быть тщательно обучены не только пониманию стандартов качества, но и методам их контроля. Это включает в себя регулярные тренинги и курсы повышения квалификации, которые необходимо проводить не реже одного раза в год. Заводам стоит также вводить внутренние тесты на знание принципов контроля, чтобы удостовериться в готовности сотрудников использовать знания на практике. При этом не менее важно обеспечить постоянное обновление оборудования, используемого для контроля. Современные технологии обеспечивают более точные измерения и могут значительно повысить эффективность производства.
Не менее значимой частью успешного внедрения является правильная организация взаимодействия между разными отделами. Важно, чтобы отделы, занимающиеся проектировкой, производством и контролем качества, работали в связке. Это позволяет снизить количество ошибок на всех этапах и быстро реагировать на возникшие проблемы. Совместная работа также даёт возможность учесть все нюансы на этапе планирования, что помогает предотвратить возможные дефекты заранее. При этом рекомендуется оформить регламенты кросс-функциональных совещаний, где представители каждого подразделения могут делиться своими «болями» и идеями по улучшению процесса.
Также крайне полезным может оказаться планирование регулярных аудитов. Это позволяет не только выявлять текущие проблемы, но и прослеживать тенденции, которые могут привести к крупным ошибкам. Полученные данные можно использовать для корректировки рабочих процессов и стратегий управления качеством. Безусловно, внедрение автоматизации является одной из самых обсуждаемых тем. Программное обеспечение для мониторинга и отслеживания качества не только упрощает ряд задач, но и минимизирует человеческий фактор. «
Как говорил Генри Форд: 'Качество — это делать всё правильно даже тогда, когда никто не смотрит.'» Этот принцип должен стать основой корпоративной культуры на любом производстве.
Несмотря на все технические и организационные аспекты, важнейшим элементом остаётся человеческий. Позитивный моральный климат на предприятии способствует высокой мотивации сотрудников поддерживать уровень контроля на высшем уровне. Для этого могут использоваться различные системы поощрений и премий за достижения в области качества. Исследования показывают, что компании, инвестирующие в развитие и благополучие своих работников, демонстрируют лучшие показатели, включая уменьшение производственного брака на 20% в среднем. Вариантами поощрений могут служить как денежные премии, так и не менее значимые — дополнительные дни к отпуску или обучение за счет компании.
И, конечно, не стоит забывать о постоянном анализе конкурентов и изучении передового опыта. В мире машиностроения каждый день возникают новые инновации, и важно быть всегда на шаг впереди. Это может включать в себя посещение отраслевых выставок, чтение профильной литературы и даже обмен опытом с компаниями из других стран. Внедрение таких практик требует готовности к постоянным изменениям и адаптации, что, в конечном итоге, делает предприятие более гибким и устойчивым на рынке. Как показывает практика, заведения, которые следуют этому пути, повышают свою конкурентоспособность и увеличивают долю рынка на 15-25% в течение нескольких лет.
Я работаю в области производства, специализируясь на машиностроении. Мне нравится исследовать новые подходы в проектировании и улучшении процессов. Пишу статьи и доклады на темы, связанные с прогрессом в машиностроении. Это дает мне возможность делиться своими знаниями и опытом с широкой аудиторией. Моя цель — сделать вклад в развитие современных технологий.
Написать комментарий