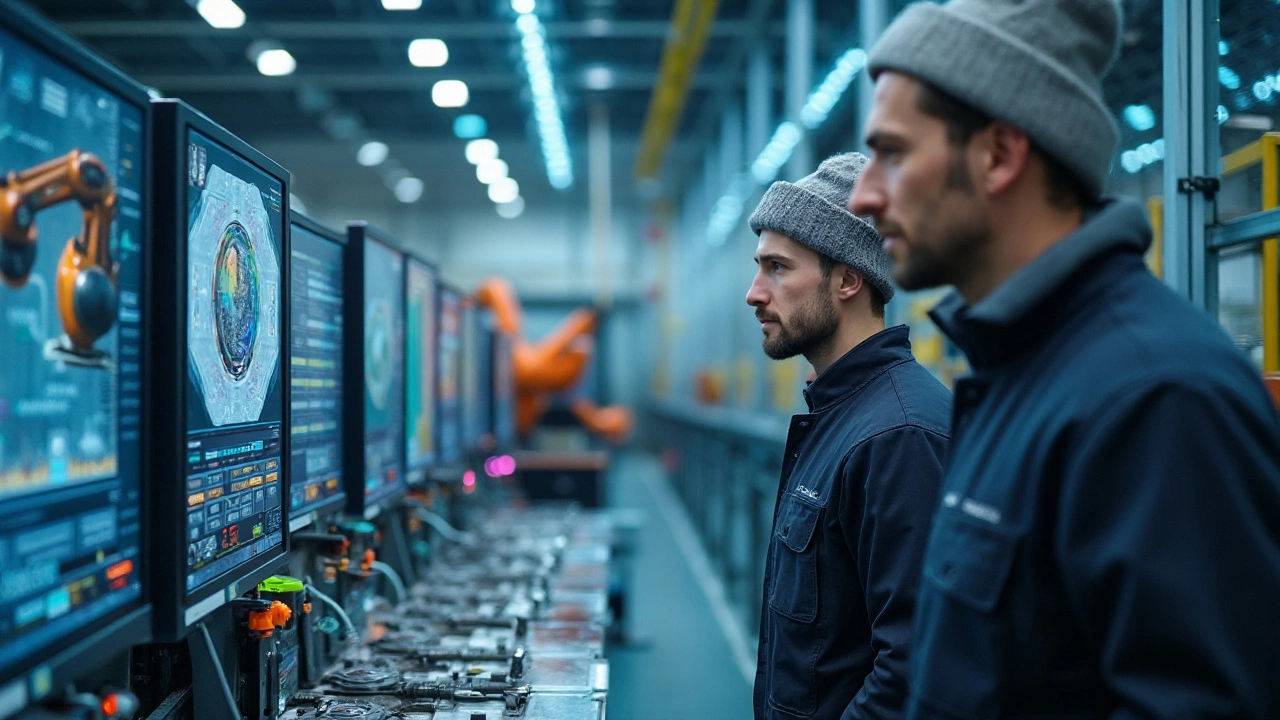
Автоматизация заводов более не является уделом только крупных корпораций. Сегодня это необходимость для всех, кто хочет оставаться конкурентоспособным в производственной сфере. Понимание фундаментальных элементов автоматизированных систем поможет улучшить эффективность и оптимизировать процессы.
Важнейшими из этих элементов считаются управляющие контроллеры, сенсоры и исполнительные механизмы. Эти компоненты взаимодействуют друг с другом, формируя основу для выполнения сложных задач.
Кроме того, понимание принципов работы каждого элемента позволяет создавать более адаптивные и настраиваемые системы, которые отвечают современным требованиям рынка. Разберем подробнее, как каждый из этих компонентов вносит свой вклад в общую автоматизированную экосистему на заводе.
Управляющие контроллеры являются мозгами автоматизированных систем на заводах, предоставляя возможность управлять сложным оборудованием и процессами. Их роль в современных производственных линиях сложно переоценить, поскольку они обеспечивают выполнение программ управления, обработку сигналов от сенсоров и принятие решений на уровне, который был не доступен традиционным ручным системам. Контроллеры позволяют достигать высокой точности и надежности работы промышленного оборудования, что минимизирует риск ошибок и сбоев.
Наиболее распространенные контроллеры в промышленности - это программируемые логические контроллеры (ПЛК), которые используются для управления машинами в сборочных линиях, обработки данных и контроля производства. ПЛК объединяют в себе функции аналогового и цифрового управления, позволяя интегрировать их в существующую инфраструктуру без значительных затрат. Интересный факт: первые ПЛК были разработаны в 1968 году для автомобильной промышленности и с тех пор стали неотъемлемой частью заводских систем автоматизации.
"Современные ПЛК способны обрабатывать тысячи сигналов в реальном времени и взаимодействовать с различными сетями и интерфейсами. Это делает их незаменимыми в крупных производственных организациях," - отмечает эксперт в области промышленной автоматизации Джон Шмидт.
Управляющие контроллеры можно разделить на несколько типов в зависимости от их функционала и области применения. Некоторые из них предназначены для работы в жестких условиях, например, для использования в тяжелой промышленности, тогда как другие специализируются на задачах, требующих высокой вычислительной мощности и памяти. Каждый из этих типов имеет свои преимущества и недостатки, и правильный выбор контроллера может существенно повлиять на эффективность всей системы. Необходимость адаптации к изменениям на производственных линиях также играет ключевую роль в выборе контроллера, который может обновляться с учетом новых требований.
Современные контроллеры поддерживают удаленный доступ и мониторинг через Интернет, предоставляя новые возможности для оптимизации производства. Это позволяет инженерам следить за производственными процессами из любой точки мира и производить необходимые корректировки. Такая гибкость и возможность быстрого реагирования стали важными аспектами в условиях глобальной конкуренции на рынке. Учитывая растущее количество данных, циркулирующих на предприятиях, среди разработчиков контроллеров особенно важным становится обеспечение безопасности информации.
Управляющие контроллеры, будучи критически важным звеном систем автоматизации, предъявляют высокие требования к качеству и надежности. Внедрение разнообразных протоколов и стандартизация интерфейсов помогают упростить их интеграцию и взаимодействие с другими компонентами. На сегодняшний день, способность контроллеров обрабатывать большие объемы данных и успешно справляться с их анализом способствует улучшению и более широкому внедрению инновационных решений на заводах. Таким образом, управляющие контроллеры становятся катализаторами изменений, которые ведут нас к заводу будущего.
Сенсоры являются неотъемлемой частью автоматизированных систем на заводах, обеспечивая сбор данных, необходимых для корректной работы оборудования. Они играют важную роль в мониторинге параметров производственных процессов, таких как температура, давление, вибрации и других критически важных показателей. Без их надежного функционирования автоматизация теряет свое значение, поскольку нет возможности отслеживать и реагировать на изменения условий в реальном времени.
Существует множество типов сенсоров, каждый из которых выполняет свою уникальную функцию. Например, термопары используются для измерения температуры и имеют широкое применение в промышленности благодаря своей высокой точности и надежности. Сенсоры давления необходимы там, где критично следить за изменением давления, например, в трубопроводных и гидравлических системах. Современные сенсоры оснащены возможностью передачи данных напрямую в системы управления, что позволяет мгновенно реагировать на изменения и поддерживать стабильность процессов.
Особую важность сенсорам придаёт тот факт, что они могут работать в сложных условиях, таких как экстремальные температуры или высокое давление, обеспечивая бесперебойный поток данных. Это достигается за счет применения специализированных материалов и технологий. Например, некоторые сенсоры могут использовать оптические или лазерные методы для измерения параметров без контакта, что помогает сохранить точность даже в агрессивных средах. Эти технологии значительно повышают надежность заводов и сокращают затраты на обслуживание.
"Сенсоры делают невидимое видимым. Они преобразуют физические явления в данные, которые можно использовать для управления системой," — отмечает профессор Иванов из Института Автоматизации.
Стоит отметить и еще одну ключевую задачу сенсоров — обеспечение безопасности. В случае обнаружения опасных изменений, таких как утечка газа или перегрев оборудования, сенсорные системы могут автоматически инициировать протоколы аварийной остановки, предотвращая аварии и защищая персонал. Таким образом, сенсоры играют не только роль наблюдателя, но и активного участника в поддержании безопасных и эффективных условий на производстве.
Тип сенсора | Основная задача |
---|---|
Термопара | Измерение температуры |
Оптический датчик | Безконтактное измерение |
Датчик давления | Мониторинг давления |
Исполнительные механизмы играют ключевую роль в автоматизации процессов на заводах, превращая команды контроллеров в физические действия. Они действуют как "мускулы" системы, выполняя задачи, которые требуют движения и силы. Представьте себе промышленного робота, поднимающего тяжелые детали или перемещающего их с одного конвейера на другой. Это и есть работа исполнительных механизмов. Они могут быть электромеханическими, гидравлическими или пневматическими, в зависимости от конкретных потребностей и условий использования.
Интересно, что примерно 60% всех поломок в автоматизированных системах случается именно из-за неправильной эксплуатации или неверного выбора исполнительных механизмов. Это подчеркивает необходимость тщательного подбора этих компонентов с учетом всех факторов, включая скорость работы, диапазон движения, износостойкость и энергосбережение. Усилия по оптимизации их работы могут напрямую влиять на производительность и снизить расходы компании. «Исполнительные механизмы — сердце автоматизированной системы. Их надежность критична для успеха всей системы», — утверждает Джон Хопкинс, инженер-консультант по автоматизации.
Для интеграции исполнительных механизмов необходимо учесть ряд факторов. Во-первых, это совместимость с остальными элементами системы, такими как контроллеры и сенсоры. Они постоянно взаимодействуют с контроллерами, получая от них сигналы и отдавая обратную связь. Это позволяет адаптироваться к изменяющимся условиям. Во-вторых, нужно обеспечить безопасность окружающей инфраструктуры и сотрудников, так как мощные механизмы могут представлять опасность при сбоях в работе или ошибках в управлении.
Современные технологии предлагают уникальные решения для улучшения работы исполнительных механизмов. К примеру, использование передовых материалов позволяет уменьшить вес и габариты, без потери в мощности. Также внедрение компьютерного моделирования в процессы проектирования дает возможность испытать механизмы в виртуальной среде до их физического создания. Это открывает новые горизонты для более экономичного и надежного производства. Инженеры могут рассчитывать на значительное упрощение интеграции таких элементов в общую систему автоматизации заводов.
Применение автоматизации на заводах невозможно без сложного взаимодействия нескольких компонентов, каждый из которых выполняет свою уникальную функцию. Управляющие контроллеры — это мозг системы, который обрабатывает данные, поступающие от сенсоров, и рассылает команды исполнительным механизмам. Например, контроллер может собирать информацию о температуре и давлении от сенсоров и на основе полученных данных корректировать работу насосов или вентилей.
Сенсоры, в свою очередь, исполняют роль чувствительных нервов системы, фиксируя любые изменения в окружающей среде или в самом производственном процессе. Они обеспечивают точные данные, которые позволяют системе работать гибко и мгновенно реагировать на любые изменения. Специальные сенсоры могут отслеживать такие параметры, как вибрация, шум и износ оборудования, предупреждая об угрозе аварии.
В свою очередь, исполнительные механизмы приводят в движение физические объекты — для них команда от контроллера служит сигналом к действию. Будь то роботы-манипуляторы, автоматические шлагбаумы или системы подачи жидкостей, все они работают в тесной зависимости друг от друга, подчиняясь единой сети автоматизации.
По данным отчета Международного союза по автоматизации: «Правильно настроенная автоматизация позволяет снизить время простоя оборудования до 30%, увеличивая при этом производительность на 20%».
Интересно, что синергия между этими компонентами может быть подвержена целенаправленной оптимизации. Специалисты рекомендуют использовать специальные алгоритмы для минимизации задержек и повышения точности взаимодействия. Такая оптимизация помогает снизить количество человеческих ошибок и увеличить безопасность на производстве, уменьшая риск промышленных аварий.
Рекомендуется регулярно проводить техобслуживание всех компонентов, чтобы гарантировать их безотказную работу. Это позволяет поддерживать уровень промышленной автоматизации и избежать дорогих простоев. Важным аспектом является и выбор правильных сенсоров и исполнительных механизмов, например, в зависимости от специфики той или иной производственной линии: иногда пригодны стандартные решения, а в другой раз понадобятся индивидуальные доработки.
Формируя систему из таких гибких и индивидуально подходящих элементов, можно достичь высокой степени надежности. Это также открывает возможности для создания комплексных решений под специфические задачи, таких как производство лекарств или высокоточных компонентов, где необходимо строгое соблюдение технологий. Такая система — это как оркестр, где каждый игрок играет свою партию, создавая в итоге гармоничную и продуктивную мелодию современной промышленности.
Я работаю в области производства, специализируясь на машиностроении. Мне нравится исследовать новые подходы в проектировании и улучшении процессов. Пишу статьи и доклады на темы, связанные с прогрессом в машиностроении. Это дает мне возможность делиться своими знаниями и опытом с широкой аудиторией. Моя цель — сделать вклад в развитие современных технологий.
Написать комментарий