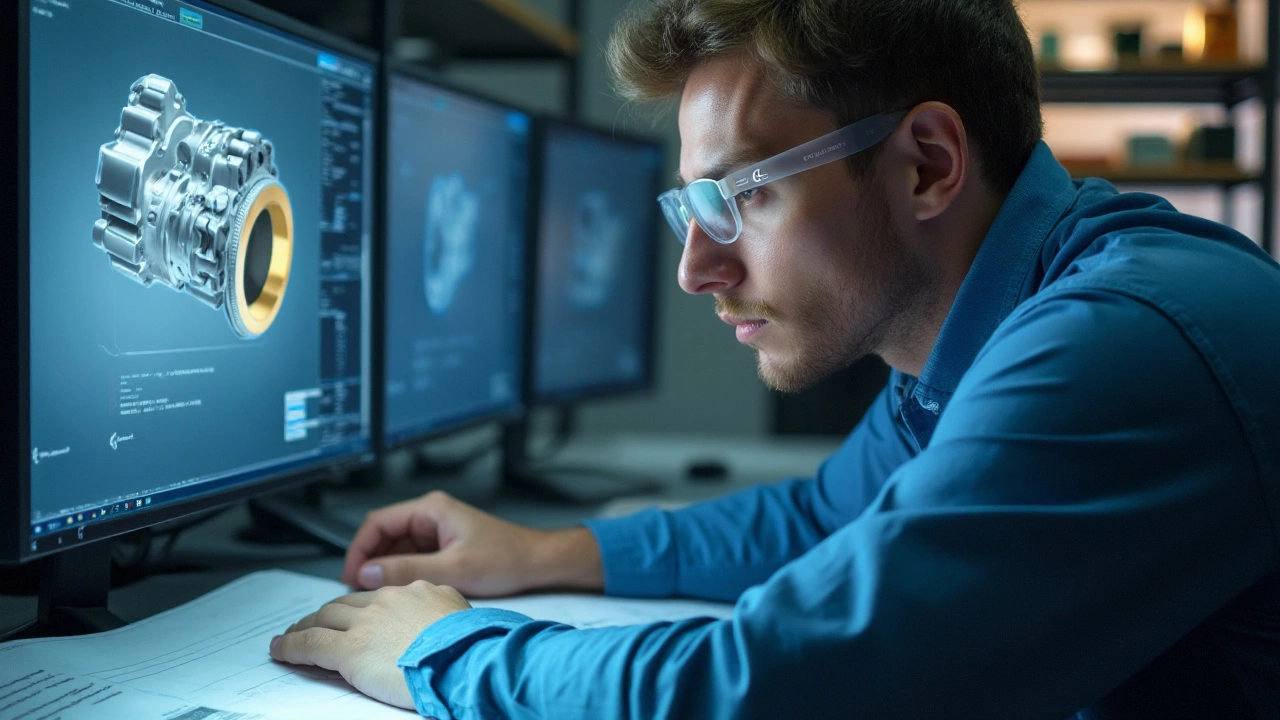
Третий этап в процессе 3D-моделирования для машиностроения представляет собой важную часть, от которой зависит качество и успех всей разработки. Здесь специалисты переходят от проектирования к проверкам и совершенствованию созданных моделей.
Критически оценивается каждая деталь, её соответствие техническим требованиям и стандартам. Нередки случаи, когда на этом этапе удаётся обнаружить мелкие недочёты, которые могли бы привести к крупным проблемам в финальной стадии производства. По-настоящему хороший инженер находит способы улучшить конструкцию, основываясь на данных анализа.
Секрет успеха кроется в использовании передовых инструментов и технологий, которые помогают изучать модели детально и вносят нужные корректировки. На этом этапе важно иметь всю необходимую информацию, советы от профессионалов и, конечно, быть готовым к исправлению любых ошибок.
Когда проект переходит в третий этап моделирования, время становится важнейшим ресурсом, поскольку именно здесь решается, будет ли модель готова к производству или нет. На этом этапе инженеры сосредоточены на поддержании баланса между точностью и экономической эффективностью, что делает его критически важным для успеха всей разработки. Машиностроение — это область, где малейшая ошибка может привести к значительным затратам, поэтому внимание к деталям здесь особенно важно.
Интересно, что именно на этом этапе можно не только обнаружить, но и внедрить инновации, которые позволят продукции выделяться на рынке. Специалисты активно используют инструменты анализа, такие как метод конечных элементов, для оценки структурной целостности и долговечности. Использование этих методов позволяет выявить слабые места конструкции и внести изменения до выпуска в производство.
"Точность – залог успеха в машиностроении. Один неверный расчёт может привести к катастрофическим результатам", — отмечает профессор Иванов из МГТУ имени Баумана.
Современные платформы для 3D-моделирования предоставляют неограниченные возможности для проведения таких оценок. Многие из них уже включают интегрированные модули для тестирования и оптимизации, что значительно упрощает работу. Это также позволяет сократить время, затрачиваемое на данный этап, увеличивая тем самым выгодность и конкурентоспособность компании. Некоторые фирмы даже составляют таблицы ошибок и корректировок, чтобы использовать их как справочную информацию для будущих проектов.
Таким образом, именно на третьем этапе создание, проверка и оптимизация становятся частями сложной головоломки, от которой зависит возможность серийного выпуска продукта. Важность правильного выполнения задач на этом этапе подчеркивается отсутствием простого исправления ошибок после запуска в производство, что делает его одним из ключевых в процессе 3D-проектирования.
Проверка соответствия модели является одной из ключевых задач на третьем этапе 3D-моделирования в машиностроении. На этом этапе инженеры детально анализируют готовую модель, чтобы удостовериться, что она отвечает всем заданным техническим требованиям и нормам качества. Это требует особого внимания к мелочам, ведь даже небольшая ошибка в конструкции может привести к значительным последствиям в производственном процессе. Хороший пример — обнаружение дефектов в моделях авиационных турбин, где возможно обнаружение ошибки массы или структуры может предотвратить потенциальные аварии.
На данном этапе важно применить различные методы проверки, включая анализ с помощью CAD-систем, которые позволяют визуализировать каждый аспект модели в деталях. Важно помнить, что софт, используемый для этой задачи, должен быть актуален и надежен. Например, системы, такие как SOLIDWORKS и Autodesk Inventor, предоставляют обширные инструменты анализа, которые позволяют симулировать условия работы модели в реальном времени, проверяя её устойчивость к различным нагрузкам.
Интересно, что для повышения точности многими инженерами применяется подход peer review, который включает проведение экспертизы модели независимыми специалистами в области проектирования. Это позволяет получить свежий взгляд на проект и выявить вероятные недочеты. Известный инженер Бенджамин Фишер однажды отметил:
"Проверка модели — это не просто этап, это обязательный элемент контроля качества, от которого зависит всё производство".
На практике, чтобы проверить модель на соответствие, инженеры нередко применяют специальное программное обеспечение для тестирования, а также проводят физические эксперименты с прототипами. Это часть сложного, но необходимого процесса, в котором участвуют как специалисты по качеству, так и инженеры, ответственные за проектирование. Важно помнить, что подобные проверки требуют не только технических знаний, но и умения работать в команде, что значительно облегчает идентификацию критических проблем на ранних этапах реализации.
Особое внимание уделяется тестированию материалов, из которых модель будет создаваться. Оптимизация предложенного материала может влиять на общую стоимость производства и долговечность конструкции. Требуется тщательная разбивка деталей на материалы с разной прочностью и износостойкостью, что сделать можно только путём комплексного анализа всех данных. Известно, что некоторые компании уделяют до 30% времени всего процесса разработке и проверке материала, чтобы гарантировать его качество и соответствие всем стандартам.
Для того чтобы проверка прошла успешно, важно учитывать все аспекты, начиная с точных расчетов и заканчивая соблюдением временных сроков. Процесс проверки модели является систематическим и требует точности на каждом этапе. Необходимо принимать во внимание требования не только клиента, но и законодательства, регулирующего производство, что особенно важно при проектировании сложных инженерных систем. Это делает третий этап моделирования не только увлекательным, но и крайне необходимым для достижения успеха. Ключ к успеху — это усердие и внимание к деталям, ведь в таком деле нет мелочей.
Оптимизация конструкции на третьем этапе моделирования — это процесс, который значимо улучшает характеристики будущего изделия. В машиностроении точность и долговечность конструктивных элементов играет ключевую роль, и для достижения этих целей применяются различные методы и подходы. В самом начале инженеры проводят детальный анализ действующих нагрузок и факторов, которые могут повлиять на моделирование. Это позволяет выявить слабые места в конструкции и избежать потенциальных проблем на этапе производства. Очень важно понимать, что благодаря тщательной проверке на этом этапе, возможна существенная экономия ресурсов и времени в будущем.
На практике оптимизация включает в себя изменение материалов, пересмотр геометрии деталей и применение новых технологий обработки. Например, использование легких, но прочных материалов, таких как композиты и современные сплавы, открывает новые перспективы для повышения эффективности модели. Благодаря компьютерным симуляциям, инженеры сегодня могут оценивать различные сценарии и выбирать оптимальные решения. Известный инженер Генри Петров отметил:
"Главное — всегда стремиться к наилучшему сочетанию минимального веса и максимальной прочности. Это не всегда легко, но именно здесь рождаются инновации."
Для достижения максимального результата, специалисты также применяют параметрическую оптимизацию, которая позволяет изменять различные параметры модели и оценивать их влияние на итоговую продукцию. Довольно распространенной практикой является разбиение конструкции и анализ её отдельных частей, что помогает более точно оценить её работоспособность и надежность. Компании, внедрившие такой подход, отмечают увеличение прочности конструкций на 15-20%, что подтверждают множественные исследования. Это становится возможным благодаря всестороннему изучению процессов, которые могут повлиять на долговечность и стабильность изделия.
Сегодня особенно популярным является применение топологической оптимизации методами конечных элементов, оптимизацию несущих конструкций для уменьшения избыточной массы и улучшения механической прочности. Инструменты, такие как ANSYS или SolidWorks, позволяют интегрировать такие методы через весь процесс 3D-моделирования, обеспечивая высокий уровень детализации анализа. Инженеры, работающие в таких программах, подбирают такие параметры, как минимальная толщина конструкции или возможные ограничения на материал, чтобы убедиться в безопасности и надежности конечного изделия.
Существует еще множество различных подходов и практик, варьирующихся от компании к компании, но все они объединяются общей целью — создать наиболее функциональную и долговечную модель с наименьшими затратами ресурсов. На этом сложном и интересном этапе можно сказать одно: каждый инженер эвристик в своем роде, делать требуется так, чтобы модель могла выдержать испытание временем и условиями эксплуатации.
Современное 3D-моделирование невозможно представить без использования сложных инструментов анализа, которые помогают не только визуализировать конструкции, но и проверять их на прочность, возобновляемость и совместимость с различными производственными процессами. В сфере машиностроения это особенно важно, поскольку от качества анализа зависит надёжность и безопасность готового продукта. С каждым годом технологии анализа совершенствуются, предоставляя инженерам широкие возможности для экспериментов и оптимизации моделей. Многие программы сегодня включают в себя модули для построения и финишного анализа, такие как Ansys, SolidWorks и другие, известные своими возможностями симуляции сложных физических процессов.
Один из основных аспектов, на который следует обратить внимание — это способность программы моделировать реальные условия эксплуатации. Это может касаться воздействия температуры, давления и других факторов окружающей среды. Программы, такие как Ansys, предоставляют возможность проанализировать эти факторы и строить прогнозы по поведению материалов в конкретных условиях.
"Правильный выбор инструментов для анализа позволяет инженерам не только улучшать текущие модели, но и создавать совершенно новые, обладающие высочайшей степенью надежности и износостойкости," — отметил в одном из интервью Антон Петров, ведущий специалист по 3D-моделированию компании Siemens.
Кроме анализа прочности и долговечности, важным аспектом является оценка производительности и себестоимости. Здесь на помощь приходят такие инструменты, как Autodesk Inventor, которые позволяют создать детальные отчёты и найти способы упрощения производственного процесса. Они дают возможность выбрать оптимальные материалы и методики, уменьшая затраты без потери качества. Использование таких инструментов позволяет инженерам сделать расчёты более точными и реалистичными.
Стоит также отметить, что инструменты для анализа в современных условиях с каждым днём становятся более доступными благодаря расширению облачных сервисов. Облачные технологии, к примеру, используются в таких системах, как Autodesk Fusion 360, которые позволяют удалённо работать над проектами в реальном времени, сотрудничая с коллегами по всему миру. Это не только упрощает процесс разработки, но и ускоряет его, значительно снижая временные затраты на обмен данными и коррекцию проектных неточностей.
Наконец, стоит помнить, что успехом подобных инструментов зависят также и от умения пользователей правильно их применять. Без глубоких знаний принципов 3D-моделирования и понимания основ инженерии даже самые мощные программы могут быть недостаточно эффективны. Поэтому важно не только осваивать программное обеспечение, но и постоянно обучаться новейшим методам и приёмам анализа.
Третий этап 3D-моделирования в машиностроении может преподнести профессионалам немало сюрпризов. На этом этапе часто скрыты ошибки, которые необходимо устранять, чтобы избежать проблем в последующей реализации. Первая из них — это несоответствие модели заявленным требованиям или стандартам. Возникает, когда изначально были неправильно интерпретированы дизайн-спецификации. Только всесторонняя проверка и тестирование позволяют выявить это своевременно. При выявлении таких недочетов необходимо пересмотреть начальные чертежи, проверяя каждое измерение и допустимые отклонения.
Ещё одной распространенной ошибкой является недоучёт производственных возможностей предприятия. Зачастую конструкция может быть идеальной на бумаге, однако не учитывает доступные ресурсы или возможности оборудования. Чтобы этого избежать, важно тесное взаимодействие с производственными коллегами. Программы для 3D-моделирования предлагают автоматизацию этих проверок, но на практике важно ручное сведение. Опытный инженер всегда старается работать в симбиозе с отделом производства, чтобы получить конструкцию, исполнимую на имеющихся мощностях.
Еще одна штука, о которой забывают — технология сборки. Проектировщик должен учесть все возможные этапы сборки и их последовательность. Ошибки здесь приводят не только к невыполнимым проектам, но и к значительным убыткам. Например, плохо проложенные детали могут стать причиной изменения всего процесса производства. Если изменить последовательность никак не получается, рекомендуется рассмотреть возможность покупки более подходящего оборудования или переспроектировать компоненты.
"Правильная работа на третьем этапе проекта может сэкономить десятки тысяч в дальнейших стадиях производства", — утверждает доктор М. Айтенберг, эксперт в области промышленного проектирования.
Важным аспектом является стоимость реализуемого проекта. Игнорирование финальных затрат может привести к перевышению бюджета. Большинство ошибок в учёте стоимости возникает из-за недооценки необходимых материалов или оборудования. Это может быть решено детальным анализом всех требуемых ресурсов и проработкой альтернативных материалов. Таблица ниже демонстрирует возможные приборы и их среднее время затраты в обработке:
Операция | Затраты времени (в часах) |
---|---|
Точение | 4 |
Мартель | 3 |
Анодирование | 2 |
Таким образом, минимизация ошибок и тщательное планирование конструктивного процесса позволит инженерам создавать более точные и экономически целесообразные конструкции. Всё это достигается тесной кооперацией специалистов и отказом от недостоверных данных, опираясь исключительно на проверенные методы и технологии.
Когда речь идет о 3D-моделировании для машиностроения, важно учитывать советы и рекомендации, полученные от опытных инженеров и специалистов. Эти знания помогают не только избежать ошибок на всех этапах разработки, но и значительно улучшить качество конечного продукта. Один из первых советов — всегда уделять внимание дизайну среды. Именно от нее зависят процессы анализа и проверки модели. Моделирование должно выполняться в комфортных условиях, что позволит избежать нежелательных накладок на качество проекта.
Специалисты советуют использовать современные программные средства, которые помогают улучшить точность и скорость работы. К примеру, пакет программного обеспечения CAD позволяет проектировать и моделировать детали с учетом всех возможных нюансов. Таким образом, на этапе третьего моделирования можно найти и исправить даже самые незначительные недостатки.
Важным аспектом является также команда. Грамотно распределенные роли и обязанности позволяют инжиниринговым группам выигрывать время и добиваться лучших результатов. Один инженер может отвечать за моделирование, другой — за проверку параметров, третий — за оптимизацию. Это способствует более углубленному пониманию задачи и максимальному вкладу каждого участника в конечный успех. Поддержка инновационных технологий также считается залогом эффективной работы.
Еще одна полезная рекомендация — проведение тщательной проверки и ведение документации на всех этапах процесса. Моделирование не лишено ошибок, которые могут проявляться из-за человеческого фактора или программных сбоев. Регулярные проверки помогут выявить их на раннем этапе. Для этого можно использовать как ручные проверки, так и автоматические тесты, интегрированные в процесс моделирования. Правильное ведение изменений в документации сразу дает понять, что было изменено, с какой целью и зачем это было необходимо.
“Не забудьте задокументировать каждое изменение, — советует Джонатан Рейс, инженер по 3D-разработкам, — это сэкономит массу времени и нервов, когда придет момент исправлять ошибки.”
На третий этап модели приходится одна из важнейших задач — улучшение. В связи с этим правильное распределение времени и усилий на данном этапе гарантирует достижение минимально возможного количества ошибок в финальной версии. Специалисты рекомендуют не экономить на времени анализа и оптимизации, ведь от этого зависит будущее надежности и долговечности конструкции. Порой лучше немного задержаться на этом этапе, чем тратить впоследствии гораздо больше сил и ресурсов на исправление несовершенств в реальных условиях производства.
Я работаю в области производства, специализируясь на машиностроении. Мне нравится исследовать новые подходы в проектировании и улучшении процессов. Пишу статьи и доклады на темы, связанные с прогрессом в машиностроении. Это дает мне возможность делиться своими знаниями и опытом с широкой аудиторией. Моя цель — сделать вклад в развитие современных технологий.
Написать комментарий