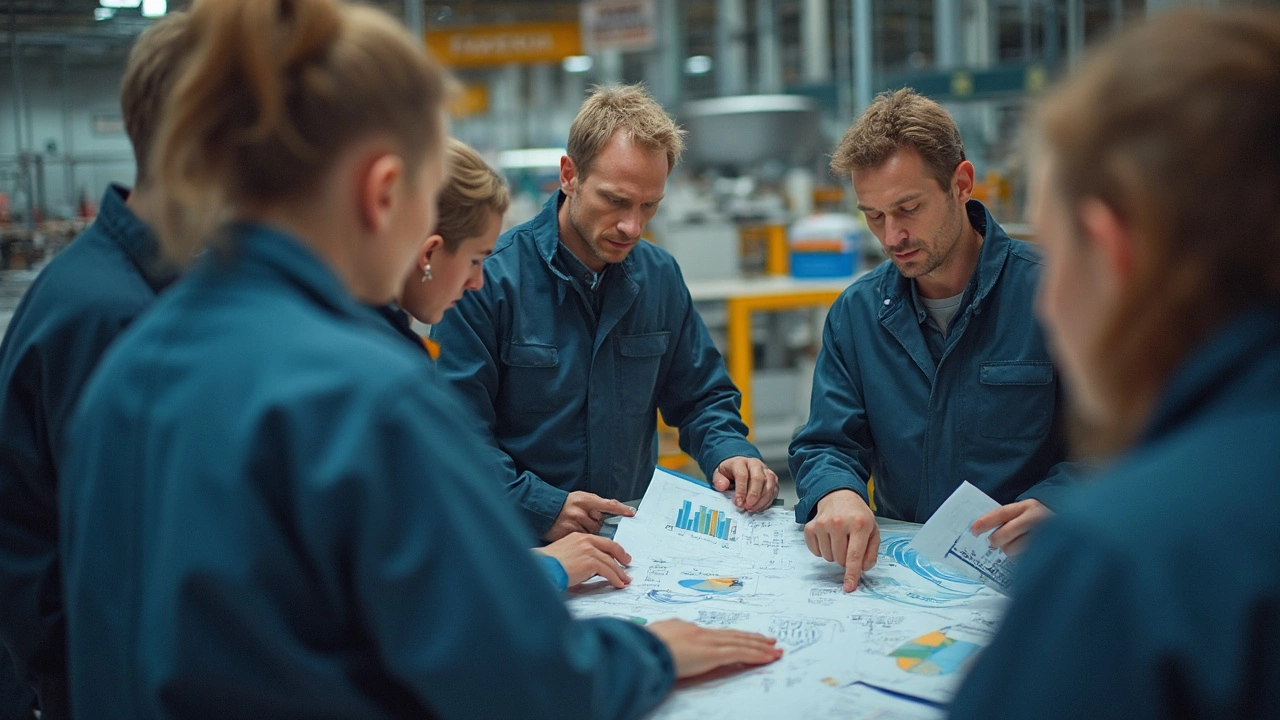
Все слышали про семь принципов управления качеством, но на практике их применяют не все. Особенно в машиностроении — где брак и задержки могут стоить много денег, времени и, честно говоря, нервов. Здесь законы просты: упустил деталь — потерял клиента. Поэтому настоящая эффективность начинается с правильной работы с качеством.
Например, один из заводов в Твери снизил количество претензий на 26% всего за год, когда начал следовать принципу вовлечённости персонала и процессному подходу. Это не магия, а логика: когда каждый работник знает, за что он отвечает и зачем нужен контроль на каждом этапе, сложные цепочки работы превращаются в понятные процессы. Отдельную роль играют клиенты: их требования — это не абуза, а точка отсчёта для стандартов предприятия.
Вы удивитесь, насколько больше можно производить при той же команде, если взять за основу принципы качества. Это не про избыточные проверки или заполнение бумажек. Это про выработку привычки делать качественно — с первого раза.
Вся суть управления качеством не в красивых лозунгах, а в измеряемых результатах. Эти принципы вошли в стандарты ISO 9001, потому что десятки лет заводы по всему миру видели: без них двигаться вперёд не получится. Особенно актуально это для управления качеством в машиностроении, где цена ошибки слишком велика.
Когда каждый процесс стандартизирован, а сотрудники понимают свою роль, количество брака заметно снижается. У исследователей из Немецкого института качества есть реальный пример: после внедрения принципа "ориентация на клиента" на среднем машиностроительном заводе число возвратов снизилось на 19% за полгода. Раньше почти каждый 17-й заказ возвращался в ремонт, после внедрения — один из 50.
Давайте посмотрим, как это работает на деле:
Сравним несколько показателей предприятий, где принципы внедрены, и где к качеству относятся формально:
Показатель | Без принципов | С принципами |
---|---|---|
Доля брака | 3,8% | 1,1% |
Средний срок выполнения заказа | 14 дней | 9 дней |
Число жалоб клиентов | по 20 ежемесячно | 5-6 в месяц |
Цифры говорят сами за себя. Без системного подхода качество быстро скатывается, а с ним — растёт лояльность клиентов и снижаются издержки.
Кажется, что все говорят о клиентах, но часто этот "фокус" ограничивается анкетами после продаж. На деле в управление качеством в машиностроении клиенты задают вектор для всех процессов. Их требования становятся планкой, ниже которой нельзя опускаться.
По исследованиям Ассоциации машиностроителей России, около 60% возвратов продукции связаны с тем, что конструкторы не учли пожелания конечных пользователей. Инженеры могут думать, что знают лучше, но именно обратная связь помогает выявлять слабые места.
Чтобы не раствориться в догадках, ведущие предприятия внедряют практики:
Вот реальные цифры из отчёта одного из крупнейших заводов Подмосковья:
Год | Возвраты по браку (%) | Количество рекламаций | Доля учтённых пожеланий (от всех заявленных), % |
---|---|---|---|
2022 | 3,2 | 124 | 58 |
2023 | 1,8 | 69 | 81 |
2024 | 1,2 | 41 | 93 |
Видно, что чем больше замечаний клиентов внедряли в производство, тем меньше было брака и возвратов. Никто не любит жалобы, но без них не получится повысить реальные показатели. Старайтесь видеть рекламации не как проблемные письма, а как бесплатную подсказку для улучшения своего продукта.
Если сотрудники на производстве не понимают, зачем нужен контроль качества, никакие стандарты не спасут. Многое зависит от того, насколько все вовлечены в процесс. В машиностроении эта вовлечённость — не просто модный термин, а реальный фактор, который можно измерить. По данным Ассоциации качества, предприятия, где персонал вовлечён в управление качеством, снижали количество внутренних дефектов на 18–25% за два года.
Что это значит для цеха? Во-первых, мнение каждого действительно слушают, даже если это просто новый слесарь. Люди отмечают проблемы, а начальство реагирует — иначе одна мелкая ошибка превращается в огромные потери. К тому же, регулярные мини-совещания помогают делиться идеями: иногда простой совет мастера приводит к экономии сотен тысяч рублей на этапе сборки.
Рассмотрим, как выглядит вовлечённость в цифрах:
Показатель | Без вовлечения | С вовлечением |
---|---|---|
Количество замечаний на 1000 изделий | 56 | 37 |
Время простоя оборудования (ч/мес) | 14 | 8 |
Сроки устранения брака (ч) | 12 | 5 |
Как добиться такого эффекта? Вот что реально работает:
Самое важное — не делать из вовлечённости очередную «галочку» ради отчёта. Здесь ценится честность: если кто-то нашёл косяк, его благодарят, а не наказывают. Только так команда начинает работать на один результат.
Многие ошибки в управлении качеством происходят не из-за некомпетентности, а потому что решения принимаются на глазок. Просто верить опыту — мало. Вот почему так важен процессный подход: все строится на понятных этапах, измеримых показателях и постоянной проверке фактов.
Процессный подход не дает провалиться в хаос — каждый шаг на производстве фиксируется, анализируется, и если появляется сбой, то точно известно, где файл случился. Сложно? Только поначалу. Когда процессы выстроены, завод экономит время, а главное — деньги.
Вот как это выглядит на практике:
Заметный пример: на челябинском машиностроительном предприятии после внедрения контроля фактов количество дефектных изделий уменьшилось с 4,3% до 2,1% за полгода. Причина — брак не уходит дальше по цепочке, потому что каждый косяк фиксируется сразу, а не потом, когда уже поздно.
Год | Дефектов, % | Объем выпуска (ед.) |
---|---|---|
2023 | 4,3 | 12 000 |
2024 | 2,1 | 13 400 |
Факты всегда сильнее догадок. Если на старте внедрять простое правило — не доверяй, а проверяй, — уже через несколько месяцев растут показатели. И это не миф: как только отдел качества начинает опираться на реальные данные, найти узкие места и убрать их становится вопросом недель, а не лет.
В машиностроении любой день без улучшений — это шаг назад. Постоянное совершенствование не про глобальные реформы, а про мелкие и регулярные шаги, которые делают производство сильнее и гибче. Если в цехах всё делают "по старинке" и никто не предлагает идей, со временем предприятие начинает проигрывать конкурентам.
Мир давно перешёл к управлению качеством, где улучшения становятся частью ежедневной рутины. Хороший пример — завод компании Toyota, который внедрил методику кайдзен ещё в 1950-х. Рабочие там сами отмечают зоны, где можно ускорить процесс или избавиться от ошибок. Это сэкономило миллионы долларов на переделках и ремонте.
Что ещё помогает не застаиваться?
Современные стандарты ISO 9001 прямо требуют постоянных улучшений. Но одни только бумажки не помогут — нужна система, в которой люди сами видят, как их идеи влияют на общий результат. Маленькие доработки изо дня в день реально меняют показатели завода, даже если это просто новый способ хранения инструмента или наглядная инструкция прямо у станка.
Такой подход гарантирует, что предприятие не скатится в рутину и сможет развиваться, даже если вокруг кризисы и заказов меньше обычного. Главное — научиться видеть не проблемы, а поводы для улучшений.
Я работаю в области производства, специализируясь на машиностроении. Мне нравится исследовать новые подходы в проектировании и улучшении процессов. Пишу статьи и доклады на темы, связанные с прогрессом в машиностроении. Это дает мне возможность делиться своими знаниями и опытом с широкой аудиторией. Моя цель — сделать вклад в развитие современных технологий.
Написать комментарий