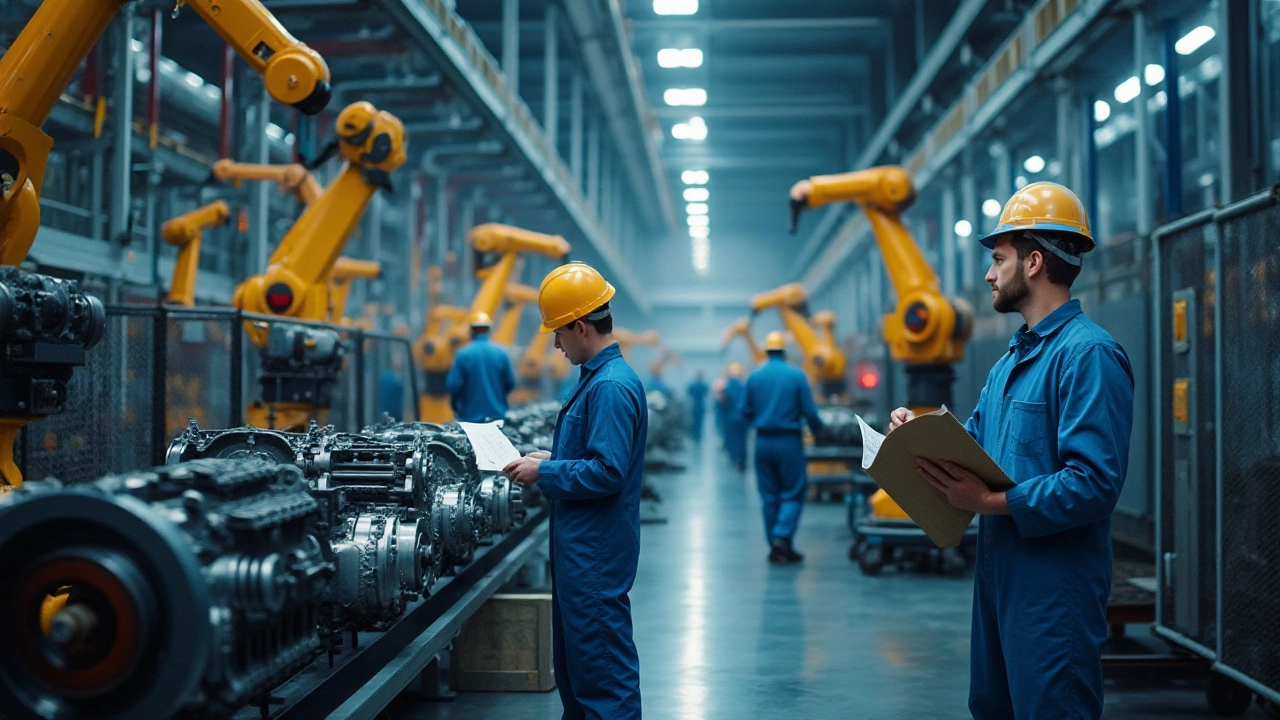
Контроль качества в машиностроении играет ключевую роль в обеспечении надежности и долговечности продукции. Этот процесс, начиная с первой чертёжной линии и заканчивая финальным тестированием, предполагает целый ряд этапов и точных методов.
Инженеры и менеджеры по качеству работают над тем, чтобы каждый компонент и каждая сборка соответствовали строгим требованиям. Это не просто механическая проверка ошибок — здесь важны внимание к деталям и аналитический подход. В этой статье мы подробно рассмотрим, как строится эффективная политика контроля качества и какие инструменты помогают ее улучшать.
Вопрос качества в машиностроении критически важен, и это не прихоть бюрократов. Контроль качества заложен в самой сути успешного производственного процесса. Чем выше качество, тем больше доволен клиент, что, в свою очередь, приводит к возврату заказчиков и хорошей репутации компании. В условиях жёсткой конкуренции на производственном рынке никто не меняет отношения к качеству как первичному аспекту.
Контроль качества — это безопасность и надежность продукции, особенно в таких отраслях, как автомобилестроение и авиация. Здесь не может быть компромиссов. Ни одна деталь, ни один компонент не должны оказаться ненадежными. Обретение доверия клиентов и, как следствие, долгосрочное сотрудничество зачастую начинается именно с качества выпускаемой продукции. Исследования показывают, что около 70% клиентов предпочитают не возвращаться к производителям, чья продукция оказалась дефектной.
Контроль качества также связан с сокращением операционных расходов. На первый взгляд может показаться, что это дополнительные расходы. Однако использование качества как основного элемента управления способствует предотвращению переделок и утечки доходов. Обеспеченные проверенные процессы, сертифицированные стандарты и контрольные испытания помогают избежать реализации бракованных изделий и экономят средства на ремонте или возврате продукции. "Качество — это бесплатный способ сделать ваш бизнес прибыльнее", — отмечал Эдвардс Деминг, основоположник современных принципов управления качеством.
Кроме того, в рамках контроля качества часто внедряются инновационные методы, что также важно в современной экономике. Использование новейших тестовых технологий и оборудования позволяет выявлять проблемы еще на стадии производства. Информация о передовых методах и инструментах поступает к производителям от технических академий и исследовательских центров, что обеспечивает непрерывное развитие отрасли.
Человеческий фактор также играет важную роль. Специалисты по качеству зачастую обладают уникальным набором навыков и знаний. Они не только наблюдают за производственным процессом, но и занимаются обучением персонала, внедрением эффективных стратегий контроля. Их вклад невозможно переоценить, ведь благодаря им устраняются риски и укрепляется система внутреннего и внешнего взаимодействия производства.
Когда речь идет об управлении качеством в такой сложной отрасли, как машиностроение, весь процесс условно можно разделить на несколько ключевых этапов. Каждый из которых имеет свои особенности и важность. Первым шагом обычно является разработка требований к качеству, основанных на конечных потребностях клиента и технических спецификациях. Это начало всех процессов контроля качества, так как именно на этом этапе формируются стандарты, которым будет следовать вся производственная цепочка. Без четкого представления конечных целей выполнение последующих этапов было бы практически невозможным.
После постановки требований наступает стадия проектирования. Цель ее — интегрировать принципы качества непосредственно в дизайн. К примеру, инженеры могут использовать автоматизированные системы проектирования (CAD) для моделирования и тестирования, чтобы предупредить потенциальные ошибки. В этот момент важно, чтобы была тесная связь между дизайнерами и производственным отделом. Все обсуждения на этой стадии основаны на данных и аналитике, что, в конечном счете, позволяет минимизировать возможные риски уже на стадии планирования.
«Изменения, внесенные на стадии проектирования, в 100 раз дешевле, чем исправления, внесенные на производственной линии», — отметил Пол Бакстон, эксперт в области качества.
Далее наступает производство, и с ним этап контролируемого процесса, часто происходящий с использованием статистических методов. Методики, такие как статистический контроль процессов (SPC), обеспечивают, что вариации в производстве минимальны, а сам процесс устойчив и предсказуем. Например, релевантные этапы сюда включается выбор случайных образцов для проверки и оценка их соответствия установленным нормам. Это помогает в выявлении систематических отклонений, которые могут повлиять на качество.
На заключительном этапе продукция проходит окончательное тестирование и инспекцию. Этот этап часто включает в себя проверку готовых изделий на соответствие всем стандартам качества и безопасности. В зависимости от сложности продукции, инспекция может быть автоматической, с применением современных технологий, или ручной. Здесь на первую позицию выходит детальное сравнение реальных характеристик продукции с изначально заложенными спецификациями. При наличии даже незначительных несоответствий могут отказать для партии или отправить на доработку, чтобы обеспечить идеальное соответствие установленным стандартам.
Заключительной частью всего процесса является анализ полученных данных и итогов контроля, что позволяет создать обратную связь для улучшения продукции. Это может быть представлено в виде отчетов или сводных данных о проведенных тестированиях. Аналогичным образом анализируются неудачи, чтобы внести коррективы и исключить их повторение в будущих сериях. Все эти этапы составляют основу эффективности любой системы контроля качества в современном машиностроении.
В современном машиностроении контроль качества — это не просто задача, это искусство. Чтобы продукция соответствовала высоким стандартам, используются разные методы и инструменты, которые оказывают значительное влияние на весь производственный процесс. Одним из мощных инструментов является метод статистического контроля процессов. Он позволяет выявлять ошибки на ранних стадиях и снижать вероятность дефектов.
Цифровые технологии открывают новые горизонты. Благодаря проверке с помощью систем компьютерного зрения, контроль становится не только быстрее, но и точнее. Это — настоящий прорыв. Например, системы машинного обучения могут, используя данные из прошлого, предсказывать проблемные области производства и устранять их до появления дефектов.
Тестирование готовой продукции также бесспорно важно. Вибрационные испытания или ультразвуковая дефектоскопия выявляют скрытые проблемы, которые невозможно обнаружить визуально. Эти методы помогают обеспечить надежность изделий, особенно в таких сферах, как автомобилестроение и авиастроение, где каждый винтик стоит денег и безопасности.
По словам эксперта в области управления качеством Майкла Харрингтона, "Только комплексный подход к контролю обеспечивает конкурентоспособность на рынке".
Использование методов неразрушающего контроля позволяет сохранять высокое качество без потерь на ресурсах. Радиографический контроль, например, дает возможность обнаруживать дефекты в сварных швах, не разрушая их целостность. При этом, такие методы требуют высокой квалификации персонала, но приносят оправданный результат в виде надежной продукции.
Помимо этого, все большее внимание уделяется интеграции систем контроля в сам производственный процесс. Это позволяет быстро реагировать на изменения и оптимизировать производственные циклы. В результате, компании, применяющие такие подходы, значительно сокращают издержки и улучшают репутацию на рынке. Ведь клиенты ценят не только качество продукта, но и надежность бренда.
Популярным также становится метод "шесть сигм", который помогает минимизировать вариативность процесса и снижать количество брака. Этот метод, основанный на сборе статистических данных и их анализе, позволяет производителям держать продукцию на уровне шести стандартных отклонений от среднего.
Для организаций, стремящихся к мировому уровню качества, важно учитывать все эти моменты. Инновационные инструменты и методы контроля качества помогают не только следить за продукцией, но и выделяться в глазах потребителей, строя долговременную репутацию.
В современном мире некачественная продукция может нанести вред не только бюджету компании, но и ее деловой репутации. Рассмотрим, как именно качество влияет на затраты и репутацию фирмы на примере машиностроительной отрасли. Когда предприятие выпускает продукцию, не соответствующую стандартам, это влечет за собой множественные дополнительные расходы. Каждая неисправность, обнаруженная уже после выпуска, требует ремонта или замены, зачастую за счет компании. Эти издержки недооценить нельзя, ведь они могут составлять значительную часть от прибыли предприятия.
Когда продукция поступает на рынок, и оказывается, что она не работает должным образом, начинается цепная реакция. Возврат брака, как правило, требует переработки всех процессов контроля и производства, увеличения затрат на создание резервных складов. Компании теряют доверие клиентов, что в конечном итоге отражается на продажах. Бренд, когда-то ассоциировавшийся с высоким качеством, начинает восприниматься рынком скептически. Наивное заблуждение, что можно сэкономить на контроле, обычно стоит потерь на сотни тысяч, а то и миллионы долларов.
"Качество — это когда возвращается клиент, а не продукция." — слова Генри Форда остаются актуальными и в наши дни. Именно за счет клиента компания продолжает свой рост и развитие.
Репутация бренда тесно связана с качеством предлагаемой продукции. Успешные компании тщательно следят за отзывами, проведением независимых тестов и внутризаводским контролем. Такие компании, как Toyota и Mercedes-Benz, за долгие годы заработали себе репутацию надежных производителей за счет исключительного внимания к качеству. Потребители готовы заплатить больше за уверенность в том, что они получают безопасную и отказоустойчивую продукцию.
Итак, как компании понимают необходимость улучшения контроля качества для снижения производственных издержек? Здесь можно выделить несколько важных шагов. Прежде всего, необходимо инвестировать в обучение персонала, который непосредственно участвует в производстве. Хорошо обученные специалисты реже делают ошибки, и, как следствие, снижаются расходы на переделку. В среднем затраты на обучение сотрудников окупаются уже через пару месяцев после внедрения программы.
Также важным фактором является внедрение современных технологий контроля. Например, внедрение интеллектуальных систем анализа дефектов с использованием искусственного интеллекта позволяет сократить брак на 30-50%, тем самым значительно уменьшив затраты. Хотя на первых порах инвестиции могут казаться значительными, в долгосрочной перспективе они возвращаются во многократном размере через сокращение потребности в дополнительной проверке и ремонте.
Метод | Среднее снижение затрат |
---|---|
Автоматизация контроля | 40% |
Обучение персонала | 20% |
Ясно, что игнорирование вопросов управления качеством в машиностроении — значит обрекать бизнес на постоянную борьбу с растущими тратами и потерю позиций на рынке. Компании, которые уделяют внимание качеству, не только сокращают лишние издержки, но и растят уверенность потребителей, что ведет их к устойчивому успеху на рынке.
Ошибки в системе контроля качества могут привести к значительным последствиям, включая увеличение затрат и снижение репутации компании. Зачастую они происходят из-за человеческого фактора или неправильной калибровки оборудования. Один из ключевых аспектов управления качеством — это выявление и исправление этих ошибок на ранней стадии. Чем раньше проблема обнаружена, тем меньше будет потеряно времени и ресурсов на её исправление.
Одна из самых распространенных ошибок заключается в несогласованности стандартов на различных производственных участках. Это приводит к тому, что конечный продукт может не соответствовать желаемым нормам. Чтобы избежать этого, важно разработать и внедрить единый набор стандартов. Нелишним будет регулярное обучение персонала новым подходам и методам контроля. Важно также проводить независимые аудиты с целью выявления вероятных ошибок еще до того, как они перерастут в серьезные проблемы.
"Качественный контроль — это не просто механизм отслеживания, а фундамент построения доверия между производителем и потребителем." — Павел Громов, отраслевой эксперт.
Еще одна серьёзная ошибка — недооценка важности регулярного технического обслуживания контрольного оборудования. Без надлежащего ухода даже самое высокоточное оборудование может давать сбои. Поэтому предприятиям стоит внедрять систематику проверок и калибровку приборов. Это поможет не только улучшить точность измерений, но и продлить срок службы высокотехнологичных устройств.
Тип ошибки | Методы предотвращения |
---|---|
Несогласованность стандартов | Внедрение единых норм, обучение персонала |
Сбои оборудования | Регулярная калибровка и техобслуживание |
Также стоит обратить внимание на коммуникацию между отделами, участвующими в производственном процессе. Порой ошибки возникают из-за недостатка информации или неправильного её понимания. Поэтому регулярные совещания и разбор контрольных показателей могут существенно снизить риск возникновения недочетов. Машиностроение требует отлаженной системы контроля на всех этапах, и только комплексный подход позволит избежать неприятностей.
Будущее контроля качества в машиностроении набирает новые обороты с развитием технологий и инновационных подходов. Одним из ключевых трендов станет использование искусственного интеллекта и машинного обучения в анализе данных. Эти технологии позволяют более точно предсказывать возможные дефекты и своевременно реагировать на них, снижая тем самым затраты и увеличивая качество продукции. В будущем мы увидим, как умные системы будут интегрированы в производственные процессы, обеспечивая оперативный обмен информацией и автоматическую корректировку настроек оборудования.
Инициативы по цифровизации, такие как промышленный интернет вещей (IoT), представляют собой ещё один значимый шаг вперёд. Смарт-сенсоры, размещенные на производственных линиях, собирают данные в режиме реального времени, помогая отслеживать статусы машин и предсказывать проблемы до их возникновения. Интеграция IoT позволяет не только минимизировать привлечение человеческих ресурсов для рутинного контроля, но и обеспечивает более высокую надежность и степень детализации контроля качества. Согласно исследованиям Forbes, предприятия, использующие IoT в процессах контроля, в среднем на 30% снижают неэффективные затраты.
"Данные — это новая нефть в области контроля качества. Те, кто умеет ими управлять, выигрывают в долгосрочной перспективе." — говорится в отчете McKinsey.
Параллельно развиваются и процессы автоматизации анализа данных, где ключевую роль играют аналитика больших данных и технологии блокчейн. Переход на блокчейн дает возможность создавать неотъемлемые последовательности событий, что позволяет более прозрачно отслеживать каждый этап производства. Это не только увеличивает доверие к системе контроля качества, но и значительно облегчает процесс аудита. Уже в ближайшие годы мы можем ожидать широкого внедрения этих технологий в отрасли. Как интегрированные системы обмена данными и аналитики смогут влиять на принятие решений, вопрос времени и усилий, которые компании вложат в их развитие.
Стоит отметить и перспективы использования дополненной реальности (AR) в сфере контроля качества в машиностроении. AR техники позволяют операторам видеть данные о машине или изделии в процессе их проверки и ремонта. Это значительно ускоряет и упрощает процесс контроля, уменьшая вероятность человеческой ошибки. В будущем такие технологии могут стать стержнем производственных процессов на заводах, поднимая уровень автоматизации и оперативности на новый уровень. Внедрение AR и VR-технологий уже становится не просто трендом, а необходимостью в некоторых аспектах.
И, конечно, нельзя обойти вниманием обучение и повышение квалификации специалистов, работающих в области контроля качества. Потребность в высококвалифицированных кадрах только возрастает, поскольку технологии становятся все сложнее и требуют понимания и управления новыми инструментами. Программы обучения должны включать в себя знания о современных технологиях и методах контроля, а также навыки работы с большими данными и аналитикой. Компании, которые инвестируют в развитие своих сотрудников, смогут не только поддерживать высокий уровень контроля качества, но и достигнуть значительных успехов на фоне конкурентов.
Я работаю в области производства, специализируясь на машиностроении. Мне нравится исследовать новые подходы в проектировании и улучшении процессов. Пишу статьи и доклады на темы, связанные с прогрессом в машиностроении. Это дает мне возможность делиться своими знаниями и опытом с широкой аудиторией. Моя цель — сделать вклад в развитие современных технологий.
Написать комментарий